De Angeli Prodotti was selected, along with 24 other companies in the Veneto region, by Fondirigenti and Confindustria to enter a list of examples of digitization and innovative management that constitute the excellence of our territory.
De Angeli Prodotti was selected, along with 24 other companies in the Veneto region, by Fondirigenti and Confindustria to enter a list of examples of digitization and innovative management that constitute the excellence of our territory.
7 managerial paradigms were analyzed that allowed these companies, including ours, to overcome difficulties and criticalities that have emerged in recent years.
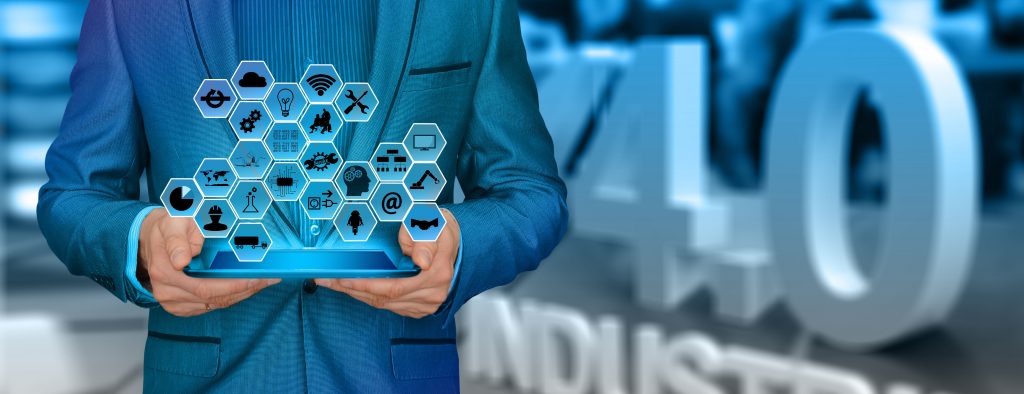
The project FABBRICHE VETRINA (Showcase Factories)
The action research carried out by the promoters of the “Fabbriche Vetrina” project aimed to describe the new managerial skills capable of overseeing the new digitization processes in companies, which very often required a non-homogeneous and linear process both from the point of view of the training required and for the type of managerial profiles used. Over the last few years, the tasks and roles of many professional figures have been transformed, including in De Angeli Prodotti.
The project presents how new generation entrepreneurs assume managerial behaviors that are more relevant and evident than in the past or how managerial profiles with high research and industrial application skills have been introduced. For many companies, digitization constitutes an enabling factor or an opportunity to radically change their business model, often adapting it to new trends related to sustainability or creativity and this constitutes – especially in a moment of extreme uncertainty such as the current one – a fundamental added value for businesses. Investment in technology has often accelerated the transformation of the business model of the company itself, setting in motion new growth opportunities.
The business cases presented, including De Angeli Prodotti, have in common the emerging nature of the digital transformation process which rests on a solid foundation of lean organization. What emerged is that often the solutions are not the result of a planned and detailed process, but the result of experiments initiated by entrepreneurs, enterprising technicians and salesmen who are careful not to neglect the innovation in the relationship with the customer.
What are the skills needed to implement management actions aimed at innovative and sustainable manufacturing?
During the research, Fondirigenti and Confindustria tried to identify the factors that influence managerial change that leads to a digital revolution. Here are the main ones:
- Mindset and digitization: it is the ability to detect new opportunities and threats, new perspectives of different stakeholders and new information or feedback from the environment that allow us to anticipate problems before they arise.
- Complexity and creativity: in a rapidly changing world, being able to orient yourself in complexity is the key to long-term success. Creativity offers a solution in terms of creating new value.
- Communication and change: the implementation of new technologies and connectivity will be “the new normal“, while constant change will be a reality that manufacturing workers – including managers – will have to deal with.
The example of De Angeli Prodotti between R&D and Enterprise 4.0
Our company was selected by evaluating various entrepreneurial and managerial variables, including the search for new materials to meet new market needs.
The project DAP 4.0
The digital innovation project undertaken in De Angeli Prodotti took the name of “DAP 4.0“. Begun in the first months of 2017 with dedicated courses of PLC programming – Controlled Logic Programmer – it has continued in the last 3 years extending to all departments. Now almost all machines are equipped with PLC devices that track, record and make available various production and monitoring data such as speed, operating time, meters produced, etc.
The goal of the project is to improve the quality of work and the individual satisfaction of all collaborators, guaranteeing customers innovative products. To achieve this extraordinary result, the IT component was added to the products and production processes. The working standards are now online and available to everyone in order to be consciously implemented, analyzed in detail with the managers, corrected with a spirit of perfectionism and, if possible, improved. Currently the production departments are equipped with TVs and monitors that show compliance with the standards in real time in the production and setup times of the machines. The production data is saved in a database and made available for reports, specific production indicators, OEE calculation and more. The project saw the participation of trainers, installers, mechanics and electricians, including external ones, with an investment of 1,350 million euros.
Having precise and real-time data, especially on machine scheduling and production times, allows us to have increasingly reliable standards that are lowered directly into production reality.
What impact did it have on the revision of the Business Model?
Demographic changes, the scarcity of raw materials and the high cost of metals are three factors that heavily affect the company’s business ecosystem, which recognizes the need to fuel investments in R&D.
There are currently several 4.0 projects in progress and plans are being made to expand the presence of PLCs and real-time monitoring in the few departments that have not been affected by the change at the moment. We are organizing to use the data collected by the machines to implement predictive maintenance, in order to avoid unexpected downtime thus improving planning and OEE.
What organizational implications were there for De Angeli Prodotti?
De Angeli Prodotti continues every day the study and research on new technologies and cutting-edge materials to create new generation products that can keep up with the demands of the market, limiting the environmental impact and increasing yields in terms of performance and customer satisfaction. For this reason, the company is looking for professionals who apply the principles of Lean Thinking with a focus on waste reduction and sustainability.
Fabbriche Vetrina: a webinar to present the research results
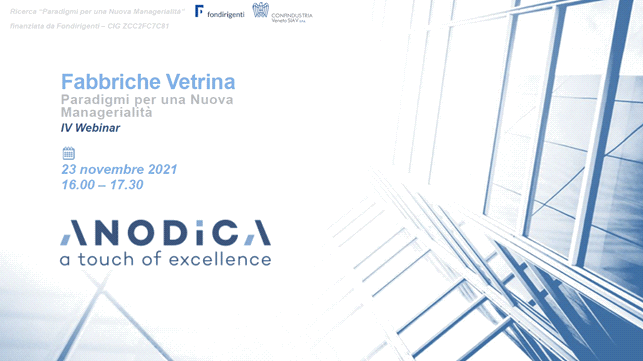
The results of the research, including the business cases in which our company is one of the protagonists, will be presented at the webinar, which will be held on 23 November 2021 from 16.00 to 17.30.
The Webinar is part of the initiatives provided for in the “Paradigms for a New Manageriality” research funded by Fondirigenti and the results of the research published online will be presented.
On the occasion of the webinar, the visit to Anodica Trevigiana Spa will be shared, it will be an opportunity for a discussion with its General Manager Giorgio Zanchetta.